Atlantic Equipment: Your Go-To Tungsten Powder Supplier
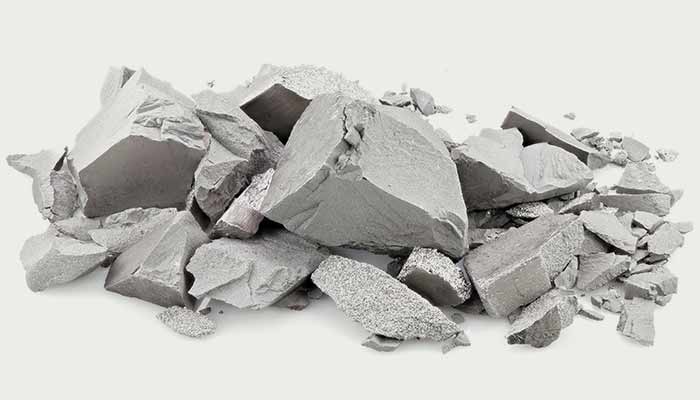
What is Tungsten Powder?
Tungsten powder is the powdered form of tungsten metal. It is gray-white in color and has the highest melting point of any metal. Physically, it is characterized by low vapor pressure, high hardness and density, and good electrical conductivity. Due to this factor, it is often used in alloys that must withstand extremely high temperatures- such as in filaments for lightbulbs. It is also used in televisions, paints, high-temperature lubricants, and many other items. Often, tungsten is alloyed with carbon to form tungsten carbide—a metal with a very high melting point and an increased hardness. Because of the high melting point of tungsten, it is most often worked within its powder state through sintering.
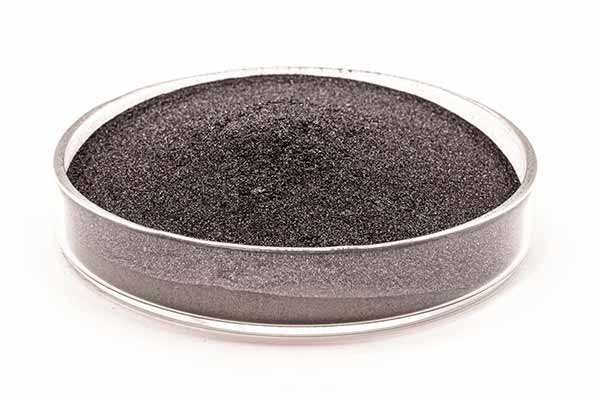
What We Offer
Atlantic Equipment Engineers has been a trusted supplier of high-purity metal powders for almost 60 years. We always prioritize quality and specialize in packing and shipping orders of any size. With AEE, you’ll always get high-purity tungsten powder that meets all your specifications at a competitive price. We offer tungsten powder in a range of forms, including a range of particle sizes, and now also in a spherical form. Atlantic Equipment Engineers guarantees fast shipping and attentive and knowledgeable customer service every step of the way.
Why Turn to Atlantic Equipment
As industry leaders, Atlantic Equipment Engineers is ready to tackle all of your high-purity tungsten and tungsten powder needs. Our commitment to excellent customer service is reflected in our industry certifications. We are proud to be an ISO 9001 certified company standard by DNV. We have experience serving a wide range of clients working in different market sectors and industries—we’re here to help you meet your business goals.
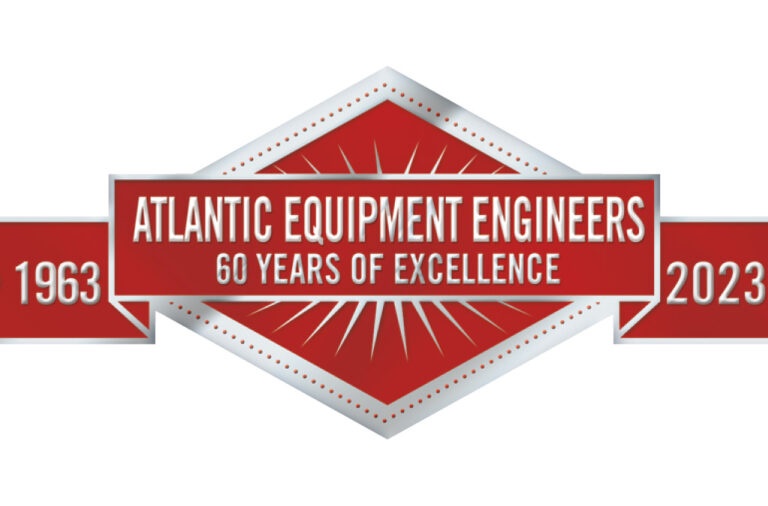
Q: How do you manufacture tungsten powder?
The manufacture of tungsten powder is a crucial step in tungsten metal, and alloy production since its properties significantly affect the properties in later operations, like sintering, pressing, and metalworking. Over 70% of tungsten throughout the world is produced via powder metallurgy. Each powder grade is made specifically for its later applications, and adherence to those stringent and exacting demands is a large part of the Atlantic Equipment fulfillment process. All tungsten powder is characterized by purity, particle size, size distribution, shape, and technological properties, which are influenced by the production process, and can be controlled mainly by the parameters applied during that process. Most of the tungsten powder produced today is accomplished by the hydrogen reduction of high-purity tungsten oxides. These oxides are placed in pusher furnaces, where the oxide powder is placed in boats which then pass through the furnace. This process offers the possibility to produce tungsten powder of almost any average grain size when the parameters of the components are altered.
Q: Will tungsten rust?
The term “rust” refers only to the chemicals that are produced when iron reacts with oxygen and water. Because pure tungsten powder contains no iron, rust is not able to develop. However, oxidation of tungsten powder can occur at varying oxygen temperatures and oxygen pressures in relation to the particle size. It is important to note that very finely divided tungsten powder is extremely flammable and can combust spontaneously upon exposure to air.
Q: Where is tungsten found?
Tungsten does not occur as a native metal. It is extracted as tungsten oxide from the minerals scheelite and wolframite. The tungsten oxides are then ground into small particles and heated with either carbon or hydrogen gas to form powder tungsten metal. The world has many tungsten reserves, mainly located in China, Vietnam, and Russia, with China being the leader in production, export, and consumption.
Q: How long does tungsten last?
Since pure tungsten is the strongest metal that can also withstand extreme temperatures, it can last indefinitely. However, pure tungsten is also highly brittle due to its extreme hardness. Making it more suitable for long-term use when alloyed with other metals.