Atlantic Equipment Engineers Supplies Custom Alloys to Partners With High-Quality Needs
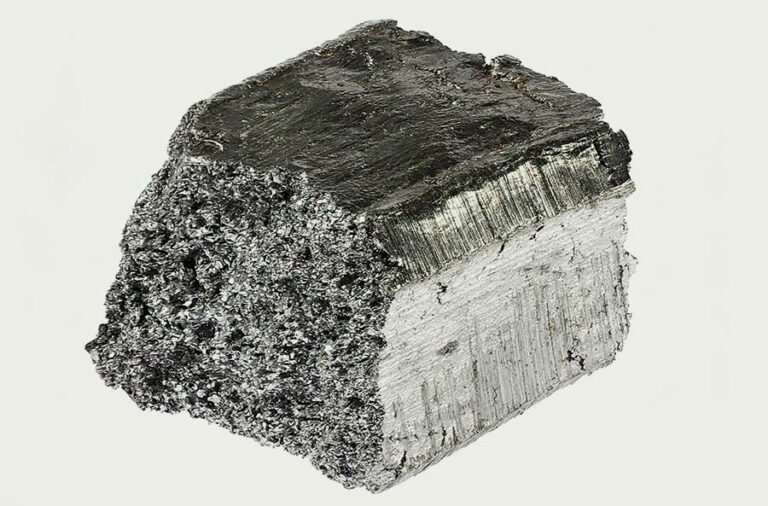
-
SS-NM-01
SS-NM-01
- Formula -
- Purity 99% - 99.5% - 99.9% - 99.95% - 99.99% - >99.99
- Particle Size 10-50 nm, 50-100 nm, 100-500 nm, 500-750 nm, 750-950 nm
-
TI-061
TI-061
- Formula NiTi
- Purity -
- Particle Size Type 1: 0-45 microns Type 2: 0-53 microns Type 3: 15-45 microns Type 4: 15-53 microns Type 5: 45-150 microns
-
NI-C276
HASTELLOY C276
- Formula C276
- Purity Ni 57%
- Particle Size 20-53 microns
-
AFA STEEL
AFA STEEL
- Formula AFA Steel
- Purity -
- Particle Size 15-45 Microns
What Are Custom Alloys?
An alloy is simply a mixture of two or more elements, at least one of which is a metal. When these elements are combined, the resulting alloy possesses different properties than its separate component parts. These properties often include advantages such as increased strength, hardness, or resistance.
Unlike standard alloys, which have a predetermined composition, custom alloys are tailored to provide unique properties suited to particular applications. These alloys are created by combining two or more metals and occasionally nonmetals in precise ratios.
Common base metals in custom alloys include iron, nickel, titanium, copper, and aluminum. The specific elements added depend upon the desired properties and ultimate intended application.
Custom alloys are developed to address specific needs such as increased strength, corrosion resistance, heat resistance, conductivity, or weight reduction. By altering the composition of an alloy, manufacturers can enhance or diminish certain characteristics as required.
These highly specialized materials are used in numerous industries, including the aerospace, automotive, medical, electronics, and construction fields. For example, aerospace components may require lightweight yet extremely strong alloys, while medical implants might need biocompatible and corrosion-resistant materials.
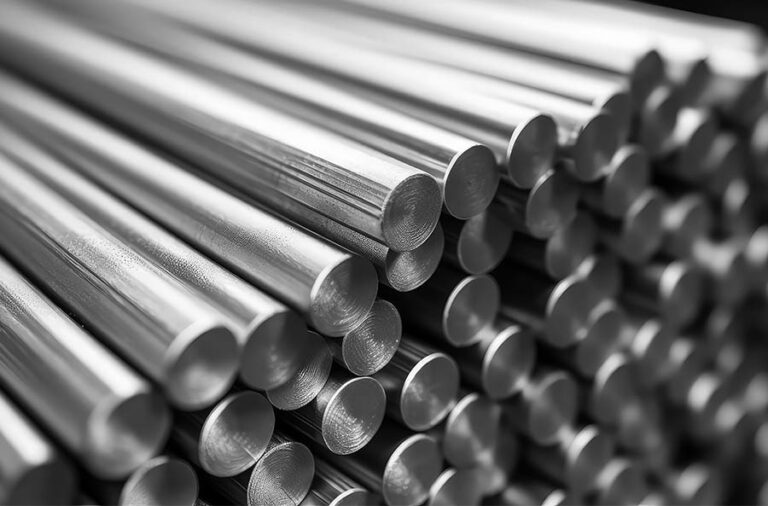
What We Offer
As one of the leading custom alloy suppliers to numerous industries across the United States, the team at Atlantic Equipment Engineers (AEE) is ideally situated to provide custom alloy solutions to clients with precise and demanding specifications. Working closely with you to understand your requirements, we can manufacture and supply a custom product to meet your needs.
With many base metals and additional components in stock, we can also offer a fast turnaround time to ensure that your processes are not delayed and that you have exactly what you need when you need it.
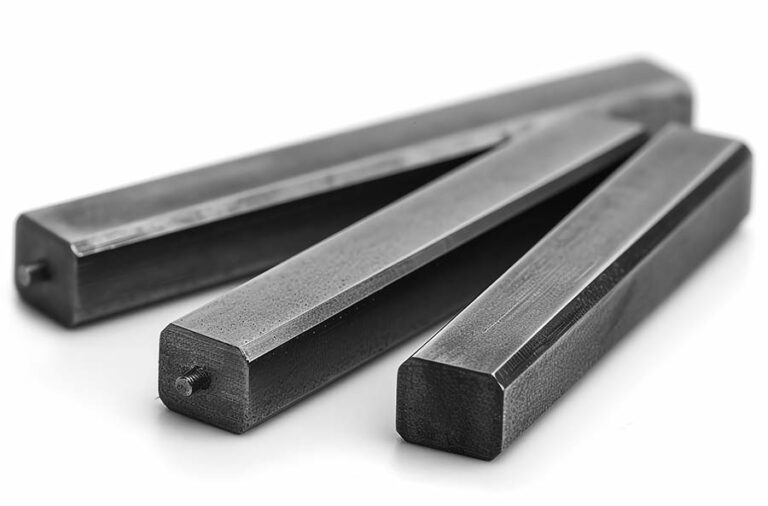
Why Turn to Atlantic Equipment Engineers?
Since its founding in the 1960s, AEE has become one of the leading suppliers of high-purity metals and metal powders and the custom alloy supplier of choice to clients in various industries across the United States and around the world.
Thanks to our certification to International Organization for Standardization (ISO) 9001 standards, you can rest assured that any custom alloys you purchase from AEE will consist of only the highest-quality component parts.
Our dedicated team of experts is always on hand to support you, offer advice, and help you develop custom solutions that will meet your needs. Our shipping is fast, safe, and secure, and our Blanket Delivery Service is designed to save you time and money.
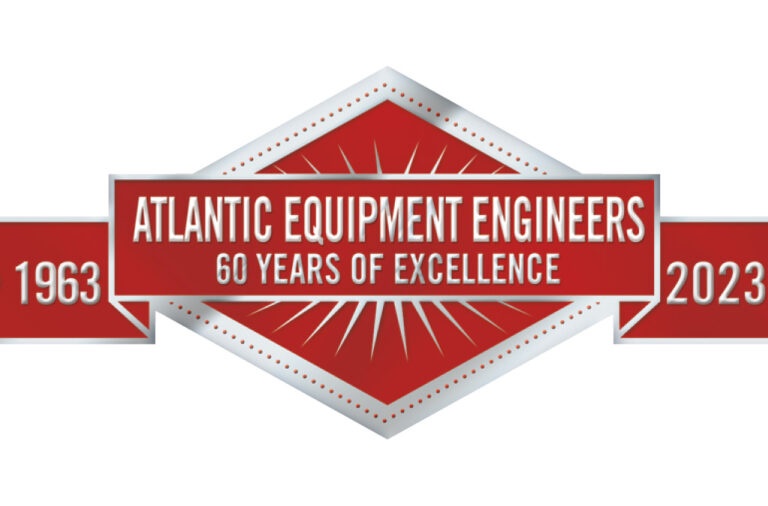
Q: What is the difference between custom alloys and standard alloys?
There are several key differences between custom alloys and standard alloys.
Also known as standard or “off-the-shelf” alloys, standard alloys are predefined mixtures with established components and composition ratios that adhere to industry standards or specifications. They provide general-purpose properties that are well understood and suitable for a wide range of applications.
Custom alloys, on the other hand, are specially formulated metal mixtures designed to meet specific requirements set by the client or the application.
The composition of custom alloys can be modified according to the desired properties, with manufacturers adding or removing certain elements or impurities to achieve specific mechanical, physical, or chemical characteristics. This flexibility allows for fine-tuning to meet performance requirements.
Conversely, standard alloys have a fixed composition that cannot be altered. They follow established standards and specifications (such as ASTM, DIN, or ISO), ensuring consistent and predictable properties. Examples you may be familiar with include stainless steel 304 and 316.
The production of custom products often involves close collaboration between the custom alloy supplier and the customer to understand the desired properties and performance characteristics. This may require specialized equipment, unique production methods, and custom testing protocols.
Standard alloys, meanwhile, are manufactured using standard production processes that have been optimized for efficiency, consistency, and cost-effectiveness, often benefiting from economies of scale.
Quality control for custom alloys is stringent. Testing procedures are often developed to ensure the alloy meets exact specifications before it is finalized and delivered to the customer. For non custom alloys, quality control follows established industry standards and guidelines, and testing is standardized to ensure that the alloy meets predefined properties and performance levels.
Q: What are the benefits of using custom alloys?
In many instances, standard alloys are more than sufficient for a given purpose. Sometimes, however, they do not offer the precise properties or functions required. In these cases, custom alloys can be customized to meet specific functional requirements, resulting in improved performance and efficiency, as well as offering greater design flexibility for engineers and manufacturers.
They can enhance the durability and lifespan of products and reduce maintenance and operational costs due to superior material properties. This can make them a cost-saving choice over the lifespan of a product or manufacturing process.
As industries evolve and demand higher and more specific performance standards than ever before, the role of custom alloys is becoming increasingly vital. Custom alloys enable manufacturers to push the boundaries of innovation and create products that meet rigorous standards and withstand ever more challenging environments.