Atlantic Equipment Engineers Supplies Hafnium Powder for Demanding Industrial and Manufacturing Applications
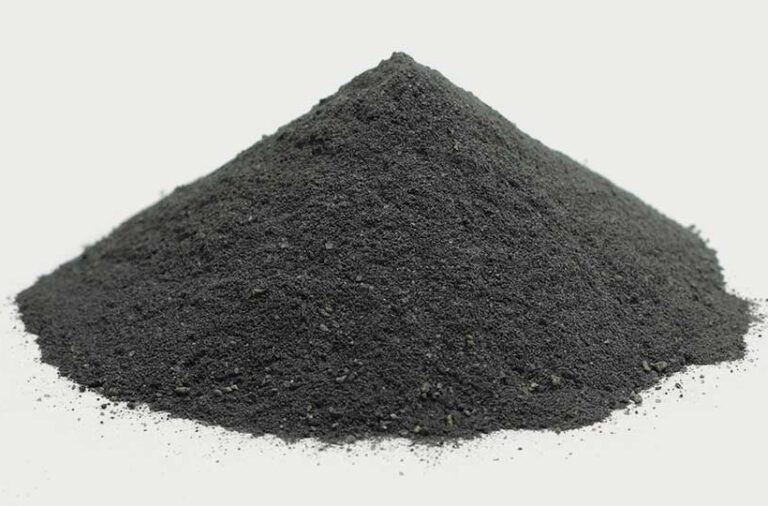
-
HF-101
HAFNIUM POWDER
- Formula 72 Hf 178.49
- Purity 99.5 min
- Particle Size -325 Mesh
-
HF-301
HAFNIUM CARBIDE POWDER
- Formula HfC 190.50
- Purity 99.9%
- Particle Size -325 Mesh
-
HF-601
HAFNIUM OXIDE POWDER
- Formula HfO2 210.49
- Purity 99.9
- Particle Size -325 Mesh
-
HF-701
HAFNIUM SILICIDE POWDER
- Formula HfSi2 234.66
- Purity 99.8
- Particle Size -325 Mesh
What Is Hafnium Powder?
Hafnium is a lustrous, ductile silver metal that, in its powdered form, is a gray metallic powder. Hafnium powder has a high melting point (2,227°C/4,040.6°F) and is prized for its excellent neutron absorption. It is also highly corrosion-resistant. These properties make hafnium powder a sought-after component for applications requiring high-performance materials for extreme environments.
Hafnium powder is utilized in industries including nuclear power, aerospace, and the manufacture of semiconductors. It is commonly used in alloys with metals such as iron, titanium, niobium, and tantalum.
Hafnium is insoluble in water or saline solutions and is not known to be toxic. However, overexposure to hafnium can irritate the eyes, skin, and mucous membranes. Hafnium powder is also highly flammable and can be explosive.
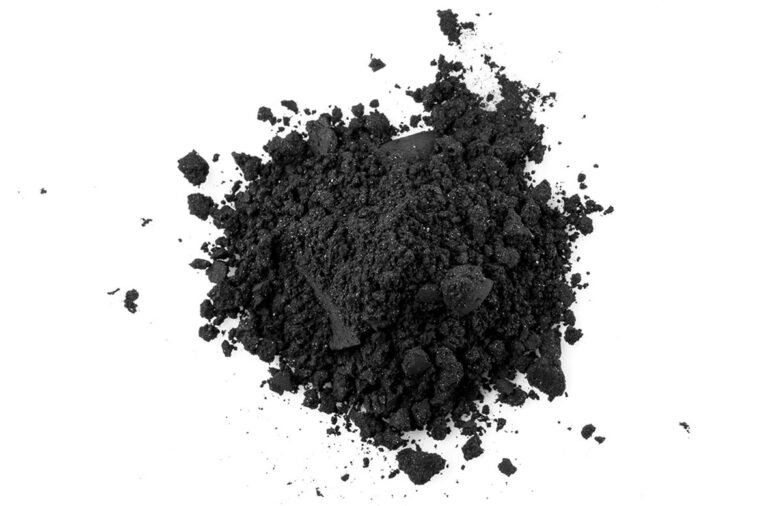
What We Offer
We supply high-purity hafnium powder suitable for use in a range of industries as well as for creating alloys with other metals. With a hexagonal crystal structure and a -325 mesh particle size, our hafnium powder is at least 99.5% pure. We also stock a range of other hafnium products, including hafnium sponge, hafnium crystal bar cutoffs, hafnium diboride powder, hafnium carbide powder, and hafnium oxide powder.
Many of our products are kept in stock for immediate shipment.
Why Turn to Atlantic Equipment Engineers
Founded in 1963, Atlantic Equipment Engineers has been a premier supplier of high-purity metals, powders, and compounds to clients all over the world for more than 60 years, with a track record of rapid delivery times, high-quality products, and competitive prices.
Our Blanket Delivery Service is designed to save you time and money. Any of our existing products can be customized to meet your requirements, and our team of experienced engineers can also advise and support you on the development of new products.
Atlantic Equipment Engineers is an ISO 9001-certified company, meaning that you can feel assured that you will receive the best possible products and service when you work with us.
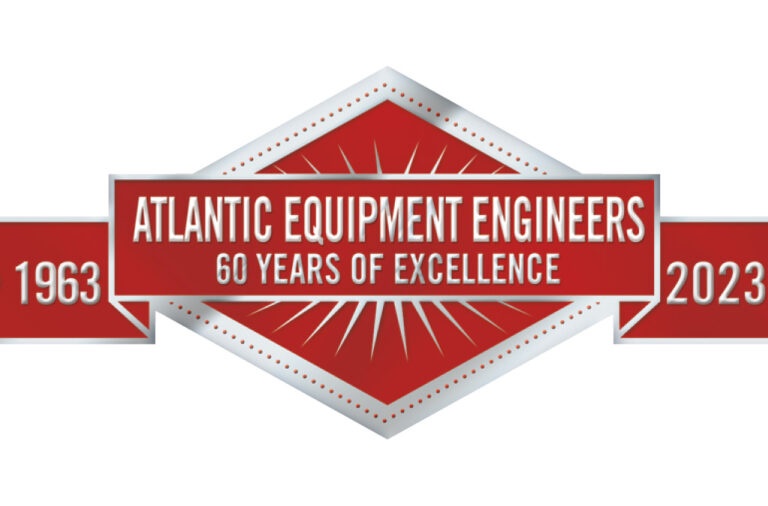
Q: What are some hafnium uses in manufacturing?
Hafnium has numerous uses across the manufacturing space and in various industries.
In the aerospace industry, hafnium is alloyed with other metals, most commonly titanium, to improve the temperature resistance and structural stability of materials. For example, the main engine of the Apollo Lunar Module is made of niobium-hafnium and titanium! Hafnium is also found in jet engines, rocket nozzles, and other critical aerospace components.
Hafnium is also added to superalloys to enhance their heat resistance and mechanical properties. These superalloys are employed in the aerospace and gas turbine industries, where extreme temperatures and pressures are encountered.
Because of its excellent neutron-absorbing properties, hafnium is an ideal material for regulating nuclear fission reactions. Hafnium is a neutron absorber for various applications, including research reactors, neutron radiography, and radiation shielding.
Hafnium dioxide is used as a dielectric material in the production of modern semiconductor devices, replacing traditional silicon dioxide due to its superior insulating properties and smaller atomic size.
During the welding of electrodes, particularly with nonferrous materials such as aluminum and titanium, hafnium helps to maintain a stable arc. Hafnium is also used in plasma-cutting equipment during metal fabrication and construction, where it serves as a cathode material. And hafnium has specialized lighting applications—it is a component in the filaments of high-performance incandescent light bulbs that are used in cinematography and high-speed photography.
Q: Are there different types of hafnium alloys?
Hafnium alloys are designed to meet the specific demands of different industries and applications, combining hafnium’s unique properties—such as its high melting point, excellent neutron-absorbing capabilities, and resistance to corrosion—with those of other metals to address various engineering challenges.
Hafnium-tungsten alloys, for example, offer strength at high temperatures and excellent corrosion resistance. They are often used in aerospace applications, such as in rocket nozzles and other components designed to be exposed to extreme heat and pressure.
Hafnium-carbide is a refractory compound that, when combined with other materials such as tantalum or tungsten, creates extremely heat-resistant materials that are also used in the aerospace industry.
Hafnium-nickel alloys are used in various specialized applications, including in the aerospace industry, where they provide enhanced creep resistance and strength at high temperatures.
Hafnium-molybdenum alloys, too, are used in applications that require strength at high temperatures and resistance to corrosion, such as in the production of jet engine components and gas turbines.
Hafnium-niobium alloys are known for their superconducting properties at very low temperatures and are used in the construction of superconducting magnets for medical equipment (such as MRI machines) and in particle accelerators.
Hafnium-zirconium alloys are commonly used in the nuclear industry due to their exceptional neutron-absorbing properties. They are also used in control rods for nuclear reactors in order to regulate fission reactions.
Q: What are the chemical properties of hafnium?
Hafnium is a transition metal with a range of chemical properties that make it valuable for numerous industrial applications. It shares its chemical structure, characterized by a dense and compact atomic arrangement with multiple electron shells, with other transition metals. Hafnium is a dense metal at around 13.3 grams per cubic centimeter (g/cm³).
Hafnium has the atomic number 72 and is represented by the symbol “Hf” on the periodic table. Its melting point is approximately 2,200°C (3,992°F), making it ideal for use in high-temperature environments. Hafnium is sparingly soluble in most acids but can be dissolved in hydrofluoric acid or aqua regia (a mixture of nitric and hydrochloric acids). It is stable at room temperature.
Among the most prized chemical properties of hafnium is its high resistance to corrosion and oxidation, making it valuable in applications where materials must withstand harsh chemical environments. It is also an excellent neutron absorber, which is crucial for its use in control rods in nuclear reactors to regulate nuclear fission reactions.
Hafnium forms a protective oxide layer when exposed to air, which prevents further oxidation. It is not as reactive as some other transition metals, such as alkali metals. Hafnium readily forms alloys with other metals, such as titanium and zirconium, allowing us to create various new materials that combine the strengths of these elements.
Hafnium-based alloys often exhibit superconducting properties at very low temperatures, making them invaluable in superconducting applications.
Q: What is involved in hafnium production?
Hafnium production is a lengthy process that begins with mining and zircon sand extraction. Hafnium is primarily extracted from zirconium minerals, with zircon sand (zirconium silicate, ZrSiO4) being the most common source. These minerals are mined from deposits, which are often found in beach sands or heavy mineral sands.
Once mined, the zircon sand is subjected to mineral separation processes to separate zircon from other minerals and impurities. These processes may include gravity separation, magnetic separation, and electrostatic separation. The separated zircon sand is then further processed to remove impurities. This may involve crushing, grinding, and washing the sand to obtain a purified zircon concentrate.
Zirconium is the primary product of this process. To extract zirconium, the purified zircon concentrate undergoes a series of chemical reactions and refining steps, including the reduction of zirconium tetrachloride (ZrCl4) to obtain metallic zirconium. Hafnium is closely associated with zirconium in its ores, and their chemical properties are similar. To produce pure hafnium, however, it is necessary to separate it from zirconium. Various separation techniques can be utilized, with the most common method being liquid-liquid extraction using an organic solvent. Once the hafnium has been separated, it goes through a purification process to remove any remaining impurities.
Hafnium is typically obtained in the form of hafnium tetrachloride (HfCl4), which is a volatile compound. This compound can be further reduced using a chemical reaction, usually with pure magnesium, to produce metallic hafnium. This reduction step takes place at high temperatures under controlled conditions.
The resulting hafnium metal is refined to remove any remaining impurities and cast into ingots or other desired forms for commercial use. Finally, the hafnium is subjected to rigorous quality control processes to ensure it meets industry standards and customer specifications for purity and quality.