Trust Atlantic Equipment as Your Go-To Tin Powder Supplier
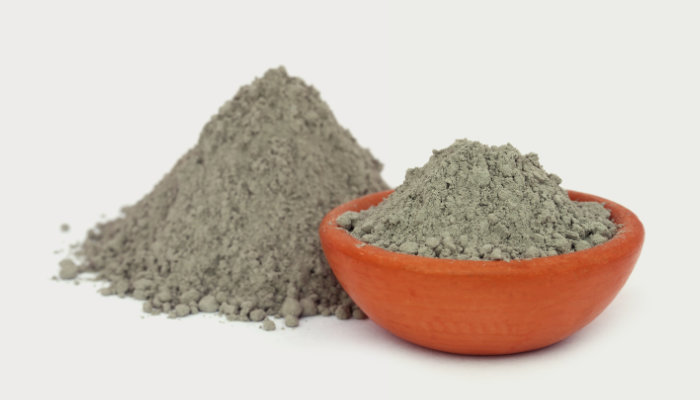
-
SN-601
TIN OXIDE POWDER, (STANNIC), WHITE
- Formula SnO2 150.71
- Purity 99.9%
- Particle Size -325 Mesh
-
SN-610
TIN OXIDE POWDER, (STANNOUS), BLACK
- Formula SnO 134.71
- Purity 99.9%
- Particle Size -100 Mesh
-
SN-NM-61
TIN OXIDE NANO POWDER
- Formula SnO2- 150.71
- Purity 99.9
- Particle Size 50-70 nm
-
SN-101
TIN POWDER
- Formula Sn: 118.71
- Purity 99.9%
- Particle Size 1-5 microns APS
What Is Tin Powder?
Tin is a chemical element that carries the atomic number of 50 and the chemical symbol Sn. It is a soft, silver-colored metal. Tin powder is produced through various manufacturing processes, including atomization, chemical reduction, and electrolysis of tin compounds.
Tin powder can vary in particle size, purity, and morphology depending on the production method and the powder’s intended application. It possesses several desirable properties, including typically fine particle size, allowing for uniform distribution and effective incorporation into various materials and processes, and high malleability, which means it can be easily deformed or shaped under pressure without cracking or breaking. This makes it suitable for forming complex shapes in powder metallurgy processes.
Tin is highly corrosion resistant, particularly in nonacidic environments, making it suitable for use in various outdoor applications and harsh operating conditions. It exhibits high electrical conductivity and is therefore an ideal material for soldering electrical connections in electronic devices and components. In addition, its excellent thermal conductivity allows it to efficiently dissipate heat in thermal management applications, such as heat sinks and electronic cooling systems.
Tin exhibits a characteristic metallic luster, making it visually appealing and suitable for applications where aesthetics matter, such as coatings and decorative finishes.
Thanks to this range of properties, tin is highly versatile. It is used in many applications across various industries, including electronics, automotive, aerospace, powder metallurgy, chemical engineering, medical devices, renewable energy, and more. Tin is also compatible with a wide range of metals, alloys, and other materials, allowing for versatile use in composite materials, alloys, and multi-material components.
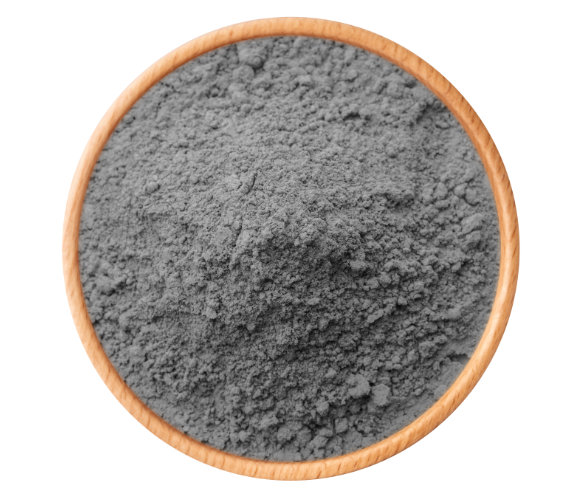
What We Offer
At Atlantic, we offer a range of tin powder products suitable for numerous applications across various industries, from automotive and aerospace to renewable energy and the medical world. Our tin powders are available in a range of particle shapes and degrees of purity, and most of them are kept in stock for immediate shipment, offering you absolute convenience. We also offer related products such as tin oxide powders and tin oxide nanopowders.
Why Turn to Atlantic Equipment Engineers
Atlantic Equipment Engineers is a leading supplier of quality and high-purity materials, including those more unusual and hard-to-find metals and metal powders. Since the 1960s, clients across an array of industries have turned to us thanks to our professionalism, high-quality products, unbeatable customer service, and commitment to providing exactly the right products at exactly the right time.
We are proud to have a dedicated and experienced team of experts on hand to assist you, and with our product customization options, we are sure to be able to help you no matter your material needs. Our Blanket Delivery Service is designed to save you time and money, and our delivery system is safe, secure, and fast.
As an ISO 9001-certified company, AEE is the go-to choice for all your metal, metal powder, and metal compound needs.
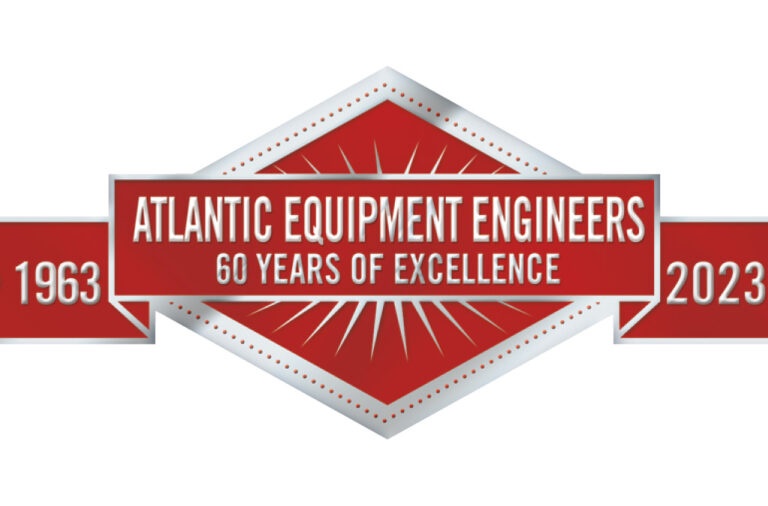
Q: How is tin powder made?
Tin powder is produced through various manufacturing processes, each designed to yield finely divided tin particles with specific characteristics tailored to the intended application. The two primary methods for producing tin powder are atomization and chemical reduction.
Atomization is a widely used method for producing tin powder, particularly for applications requiring fine particle size and high purity. To begin the process, high-purity tin metal is melted down in a controlled environment such as a vacuum induction furnace or inert gas atmosphere. This ensures minimal oxidation and contamination.
The molten tin is then rapidly atomized into fine droplets using techniques such as gas atomization or water atomization. Gas atomization involves spraying the molten tin with a high-pressure inert gas such as nitrogen or argon, causing it to break up into small droplets. Water atomization uses a similar principle but employs water instead of gas as the atomizing medium. The atomized tin droplets quickly solidify as they cool, forming spherical or irregular-shaped tin powder particles.
With atomization, the tin powder’s particle size distribution and morphology can be controlled by adjusting parameters such as atomization pressure, temperature, and cooling rate.
The chemical reduction method for producing tin powder is utilized for applications requiring larger particle sizes or specific particle shapes. A tin compound, such as tin oxide (SnO2) or tin chloride (SnCl2), forms the starting material for the process. These precursors are typically obtained from tin ores or recycled tin sources. The tin precursor is then reacted with a reducing agent, such as hydrogen gas (H2) or carbon monoxide (CO), at elevated temperatures in a controlled atmosphere. This reaction reduces the tin compound to elemental tin metal.
The reduced tin metal is then precipitated or collected as fine powder particles through methods such as filtration, sedimentation, or centrifugation. The resulting tin powder may undergo additional processing steps, such as washing and drying, to remove impurities and residual reactants.
Both the atomization and chemical reduction methods of producing tin powder offer advantages and can be tailored to produce tin powder with specific particle size distributions, morphologies, and chemical compositions. The choice of production method depends on various factors, including starting materials, desired powder characteristics, production scale, and cost considerations.
Q: What kind of applications is tin powder used for?
Tin powder is found in a wide array of industries and applications.
Tin powder is widely used in the electronics industry for soldering and brazing applications, creating electrical connections in electronic components and circuit boards.
In the automotive industry, tin powder is also used for soldering electrical connections, manufacturing sensors, and producing powder metallurgy components in engine parts and transmission systems.
In the aerospace sector, tin powder is again employed for soldering critical electronic components. It is also used in manufacturing lightweight structural components and producing specialized coatings for aerospace materials.
Tin powder is a key material in the powder metallurgy industry, where it is used to produce sintered components such as bearings, gears, bushings, and other mechanical parts with enhanced strength and wear resistance.
Tin powder serves as a catalyst in various chemical reactions and processes, including organic synthesis, petrochemical refining, and environmental remediation.
In the packaging industry, tin powder is prized for its use in producing metallic inks, coatings, and finishes for packaging materials, enhancing their aesthetic appeal and durability. Similarly, it is used in the formulation of coatings, paints, and pigments for applications in architectural, automotive, and industrial settings, providing corrosion protection, color stability, and decorative finishes.
In the renewable energy sector, tin powder is used to produce photovoltaic cells and solar panels, which facilitate electrical conductivity and enhance energy conversion efficiency.
Tin powder also has applications in the manufacturing of medical devices, including implantable devices, surgical instruments, and diagnostic equipment, where its biocompatibility and corrosion resistance are advantageous.
Finally, tin powder is utilized in the telecommunications industry for soldering connections in telecommunications equipment, such as antennas, transceivers, and networking devices.